The rough stuff department is where the soles are worked on. A number of processes are carried out here:-
Tempering
Correct preparation cannot take place unless the material is tempered, which is an important operation in the preparing department.
All cut parts are not of the same substance, quality and flexibility and so do not require the same tempering.
Tempering is done by placing the cut parts into a tank of water long enough for the soles to take in the water which loosens the fibres and renders the part workable in the various subsequent operations.
Grader and Leveller
This is one of the most labour saving machines in the rough stuff department. It will sort the substances of cut parts and make them level. It is so finely made that it can grade to 192th part of an inch. It has two sets of rollers, a front set and a hind set, at the back of which there is a knife. Between the rollers there is a chain which is spiked so as to grip the cut part to take it through the machine. At the front of the fore rollers is a gate which automatically opens and shuts.
Procedure: A cut part is pushed through the open gate which immediately closes when the part has entered. The sole passes through the front set of rollers and the feelers feel for the thinnest substance of the cut part. It is then taken by the chain further into the machine and stamped to that grade, and as it passes through the hind rollers, the knife cuts off the surplus material and the gate at the front opens ready to take the next cut part.
Rounder
There are two types of rounder:
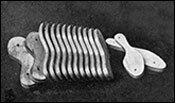 |
Wooden rounding blocks sold by BUSMC Accessories
|
|
Both work on the same principle. The machine has a big iron base, a revolving table and a big arm. A set of wooden rounding blocks are needed for the various shapes and sizes. The required block is fixed onto the machine and a sole, middle or insole can be clamped onto the block by means of the arm which is worked by a pedal.
A knife arrangement on a pivot fixed to the table is placed against the edge of the block and the block, causing it to trim off the sole to take the shape of the chosen block.
Channelling
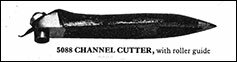 |
A channel cutting knife illustrated in the George Barnsley and Sons catalogue
|
|
This is an important operation because it will either make or marr the end shoe. Bad channelling makes for bad stitching. Knives need to be well cared for, and different ones are needed for different channels.
For stitching the channel should not be more than 1/8” from the edge or in depth. For machine sewn the channel should be ¼” from the edge, and as deep as possible. For screwed work a long shallow channel is required, about ¼” from the edge
Moulding
Moulding determines the shape of the shoe and if a sole is moulded properly it will keep its shape whatever handling it goes through.
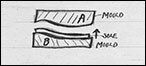 |
Drawing showing how the Sole moulder worked
|
|
The Apex Sole Moulder consists of two moulds, one for the left foot and one for the right foot. The mould A is a fixture but mould B rises up towards it. The sole is placed on B and the operator starts the machine so that B rises up to A, pressing the sole into shape. There are two sets of moulds working alternately so the operator puts one sole in and pulls one out.